ベストオブブリード型で無理なく効率良く
日本の製造業の競争力強化をデジタルで支援
TACTICS-1
国内の製造業のデジタル化が遅れており、それがグローバルでの競争力低下を招いていると指摘されることが多い。もちろんデジタル化と競争力の向上はイコールではない。では競争力の向上に有効なデジタル化とは何か、どのようなシナリオがデジタル化を進めやすいのか、海外と日本のデジタル化の違いは何か、日本の製造業に最適化されたSCMおよびPCM(原価管理:Product Cost Management)を中心に基幹業務システムを開発、提供するビジネスエンジニアリングに話を伺った。
海外製品は主に財務情報の取得が目的
国産製品は業務の効率化による競争力強化が目的
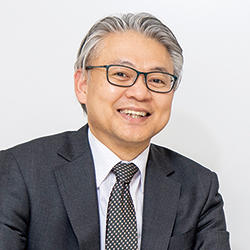
プロダクト事業本部
営業本部長
小野修司 氏
ビジネスエンジニアリングは大手・中堅企業向け基幹業務システムの開発、販売、構築、導入コンサルティング、サポートを手掛ける。同社の代表的な製品は製造業向けビジネスプラットフォームの「mcframe」で、自社開発製品のほかにもSAP製品をはじめとする海外製パッケージなどの販売、構築、導入コンサルティングも行っている。
同社は売上高の80%以上が製造業であり、その導入先のほとんどが国内企業とその海外法人で、売上規模は数十億円から数千億円と幅が広い。同社は顧客の要望に応じて、自社開発パッケージと海外製パッケージの両方を提供している。
製造業向けパッケージについて国産製品と海外製品との違いはどこにあるのだろうか。同社のプロダクト事業本部で営業本部長を務める小野修司氏は次のように説明する。まず海外製パッケージについては「欧米はトップダウン文化のため、財務諸表のリアルタイムな把握に焦点を当てており、業務プロセスについてはパッケージの標準仕様に合わせてもらうことを前提にしている傾向があります」と話す。
一方、国産パッケージについては「日本では仕事は尊いものという文化があり、現場の創意工夫を大事にする考え方のため、業務のバリエーションや自社の競争力を引き出すための要望に柔軟に応えられることに焦点を当てる傾向があります」と話す。
ただし、海外ではパッケージを標準で使う、日本ではパッケージをアドオンするという認識があるが、この考え方には一部誤解もあるようだ。
小野氏は「欧米や中国ではIT人材を社内に抱えており、アドオンやサブシステムの開発を社内で行っているケースが多く、パッケージを標準で購入しているけれども標準のまま利用しているわけではなく、手を加えたシステムを利用しています」と指摘する。
一方「日本ではIT人材を社内に抱えず、ベンダーにアウトソーシングする文化のため、アドオンされたシステムを購入するのが一般的です。手を加えるという点においては双方に違いはないのですが、日本ではアウトソーシングのため、顧客の要求を実現するためにバージョンアップに対応できないようなアドオンを加えてしまうこともあり、アドオン自体は悪ではないものの、『アドオンは悪』と語られる要因になっています」と指摘する。
また「日本では終身雇用が残っているため、長年にわたって同じ人が同じ現場、同じ業務に携わり、その人の能力に依存して業務を成り立たせている傾向があります。いい意味ではプロなのですが、その人に依存して属人的、個別最適に陥っているならば、システム化するうえでは業務プロセスの整理から行わないとパッケージの仕様に適合しません。ルールが複雑なのでアドオンも高難度なものが多発し、システム外で運用しないと業務が処理できなくなるなどの要因で、システム導入効果が限定的になることもあります。そのため、アドオンは悪とした上で、業務整理に注力すべきだという意見もあります」と補足する。
一方「海外では転職を頻繁に繰り返してキャリアアップする文化のため、人が変わる前提で業務を組む必要があります。人に依存して効率化を図るのではなく、なるべく業務を標準化してシンプルにし、またCoE(Center of Excellence)といった業務改善を主導する部署も存在するなど、パッケージの標準仕様との適合性が高くなります。担当者も自分がその業務に専属し続けるとは思っていないので、日本ほど強いこだわりはなく、会社の決めたルールに従う傾向があります」と語る。
ベストオブブリード型で
ペースレイヤリングに対応
ビジネスエンジニアリングが開発、提供するmcframeは中堅の製造業を中心に大企業まで約700社以上の導入実績を誇り、その顧客も組立加工系、プロセス系、流通・サービスなど幅が広い。また国内企業の海外拠点への導入もアジアを中心に多くの実績がある。mcframeが国内企業に受け入れられるのは国産製品というだけではないようだ。その優位点としてmcframeが「ベストオブブリード(Best of Breed:適材適所)型」で開発、提供されていることが挙げられる。
海外および国内でも広く導入されている海外製ERPパッケージは「オールインワン型」で開発、提供される。そのため導入が大規模になりがちで、コストの負担が大きくなりやすい。
もちろんオールインワン型のメリットも多くある。異なるベンダーの異なるシステムを連携させる場合、従来はAPIが公開されていない、扱えるデータの形式が異なるなど、開発の難易度が高かった。そのため複数の異なる業務を連携させたい、全社規模で業務やデータを管理したいという要望に対して、オールインワン型でシステムを統一することは有効な手段だった。
しかし現在はデータのやりとりさえできれば、異なるベンダーの異なるシステムを連携させて全体最適なシステムを容易に実現できる。また「ペースレイヤリング」への対応という観点もある。詳細は省くがペースレイヤリングとはガートナーが提唱する方法論で、業務環境と対応するシステムの変更の頻度(ペース)を指標に分類する考え方だ。
例えば財務会計システムは制度が大きく変わらない限りシステムを大幅に刷新する必要はなく、変更ペースは遅い。しかし生産管理は業務改善に伴い変化が求められ、変更ペースは速い。さらにIoTやAIなどの最新テクノロジーを利用したシステムの場合は、最初から正解が分からないためトライアルを重ねる必要があり、変更ペースは非常に速くなる。
これらの異なる変更ペースのシステムをオールインワン型で実装すると、全体最適なシステムを実現することが難しくなる。例えばオールインワン型のERPでは財務会計を中心に生産、販売、在庫、購買の管理、さらに人事給与などの機能が提供されるが、変更ペースが遅い機能と速い機能を一体化してしまうと、変更する際の範囲や影響が大きくなり、変更しづらい仕組みになってしまう。
そもそもオールインワン型は大規模導入が前提となるため、製造業の中堅、中小企業にとって導入しづらかったわけだが、市場の変化や業務改善に対応するのも大掛かりとなると、二の足を踏んでしまうのは仕方のないことだ。こうしたことも国内の中堅、中小の製造業のデジタル化のペースが遅い要因と言えよう。
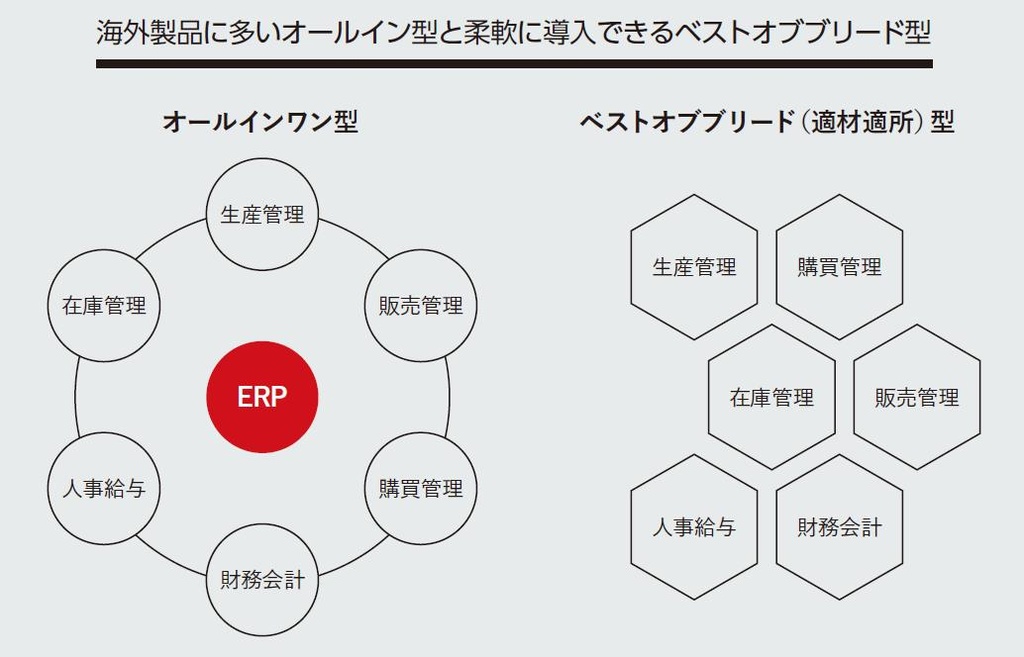
SCMを中核に連携機能を拡張
運用中の財務会計と連携導入
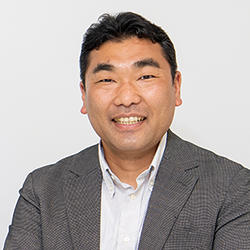
プロダクト事業本部
プロダクトコンサルティング部長
吉原一記 氏
ベストオブブリード型は例えば製造業のシステムに求められる生産管理、販売管理、購買管理、人事給与、財務会計といったそれぞれの機能を別々に疎結合で導入できる。このベストオブブリード型を採用しているmcframeでは、提供される全ての機能を導入する必要はなく、顧客の要望や事情に応じて必要な機能だけを選んで導入できることが大きな特長だ。
同社プロダクト事業本部 プロダクトコンサルティング部長 吉原一記氏は「mcframeはSCM領域に特化したパッケージのため財務会計機能を持ちませんが、代わりに財務会計システムとの連携機能を用意しています。財務会計システムを持たない企業はありませんので、mcframeを導入することで生産管理・販売管理・原価管理といったSCM領域を強化しつつ、既存の財務会計システムと連携して、導入対象を絞りつつ全体最適なシステムを構築できます。例えば日本の本社は使い勝手が良くリーズナブルな国産の会計パッケージ、海外拠点はmcframeシリーズの『mcframe GA』で統合、大手企業なら海外製の会計パッケージでグローバル統合するなど、お客さまのニーズに応じた会計パッケージの選択が可能です。さらにIoTやPLM領域のラインアップもありますので、継続的に拡張・進化させることができます」と説明する。
mcframeはSCM機能を提供する「mcframe 7」を中心に、海外拠点向けERP「mcframe GA」、データ分析・可視化ソリューション「mcframe COCKPIT」、PLMソリューション「mcframe PLM」、そしてIoTソリューション「mcframe IoT」などをラインアップしている。
mcframeシリーズで中核となるmcframe 7は生産・販売・原価管理領域に特化したSCMソリューションだ。日本の商習慣や多様な物流・商流モデルに対応し、多言語・多通貨対応、複数拠点・複数会社対応により、国内だけでなくグローバルでの利用も可能だ。見込生産・受注生産など各種生産方式への対応やタブレットによる実績把握、品目別の実際原価・損益分析、他システムとの連携など、さまざまな顧客への導入で培われた各種業務への適応や運用ノウハウが反映されており、日本の製造業に最適化されていることがmcframe 7の魅力となっている。
またmcframe 7には納期遵守率や原価・在庫分析などのKPI、次のアクションを促すプッシュアラート、操作性の高い画面設計など、業務の迅速化、効率化を促進するさまざまな仕組みや工夫も提供されている。
さまざまなシステムと連携できるmcframe 7だが、mcframe 7の活用によって生み出されるデータを管理する環境の柔軟性も高い。現在はOracleとPostgreSQLに対応しており、連携できるデータベースを今後も広げていく予定だ。
吉原氏は「mcframe 7のマルチデータベース化を進めており、第一弾としてPostgreSQLに対応しました。クラウドの利用が拡大する中で、メジャーなパブリッククラウドでPostgreSQL互換データベースサービスが提供されるようになっているからです」と説明する。
mcframeシリーズ間の連携にも力を入れている。海外拠点向けERPのmcframe GAと連携することでグローバルERPの構築ができるほか、設備管理ソリューション「mcframe SIGNAL CHAIN」との連携で製造業務を縦串でつないだり、データ分析・可視化ソリューションのmcframe COCKPITと連携してmcframe 7のデータを束ねて意思決定に役立てたりできるなど、国内製造業の競争力強化に役立つソリューションを充実させている。
吉原氏は「IoT・PLMなどmcframeシリーズの各製品に加えてアライアンス製品と連携しやすくすることで、導入したら終わりではなく、継続してお客さまの業務・システムの進化・拡張、DX化に貢献したいと考えています」とアピールする。
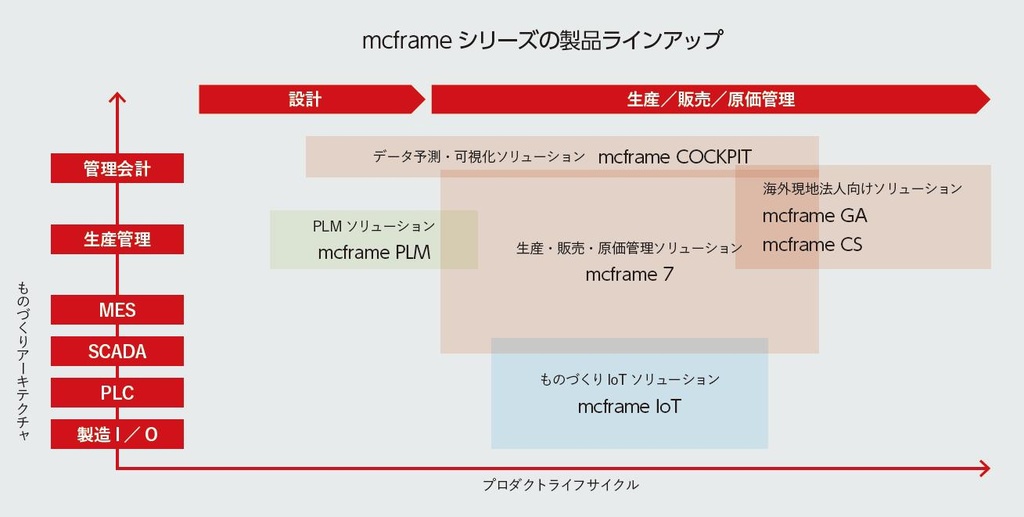
パッケージを導入してデータ化
業務をパッケージに合わせて標準化
デジタル化による競争力強化が求められている日本の製造業に対して、どのようなアプローチで取り組みを促進すればよいのだろうか。吉原氏は「システム化されておらず、Excelや手書きの伝票で運用されているようなお客さまに対しては、まずはパッケージが持つ標準業務フローをお手本に業務を整理して、使えるところからシステムを活用することで基本的な数字をデータ化して蓄積することを提案しています。これによりKKD(経験・勘・度胸)ではなく、データに基づく判断が可能になります。次のステップとして自社の経営の強化や業務の効率化にどのような機能・データが必要なのかを見極めて、運用の改善や機能強化、必要なソフトウェアの追加導入を実施します。いずれにしても自社がどうなりたいのか、どうしたいのか、その目標を達成するための仮説を立てて推進していくことが重要です。挑戦は良いことですが、仮説がなければ挑戦の結果を評価することはできませんし、次のステップにもつながりづらいです。最終的なゴールをイメージしつつ、段階的に拡張していくことが、無理なく効果を体感しやすい方策です」とアドバイスする。
小野氏も「お客さまへの提案時によくお話するのですが、生産管理の導入が目的ではなく、導入することで得られたデータを経営や現場改善に生かすことを目的として、データを蓄えるために生産管理を導入するのです」と話す。さらに「データをどう扱うのかということに加えて、現状の業務をどう変えていくのかということも大切です。その点においてもパッケージの導入が効果的です。現状の業務をパッケージに合わせることで、変えることができますから。このような目的でmcframeを導入するお客さまも増えています」という。
実際にmcframe 7のSCMおよびPCM(原価管理)を導入して業務を見直した事例を紹介する。売上高400億円、従業員数が単体で500名、連結で3,500名の機能化学品や機能樹脂、電子素材、フィルム、ステッカーなどの幅広い製品を展開する国内の企業では基幹業務システムを刷新し、その基盤にmcframe 7を導入した。
同社は構築から30年以上経過した基幹システムを運用していたが、システムの老朽化に加えてシステム間の不整合により変化対応が困難となり、また内部統制の観点から監査認証取得に必要な機能が不足していたなどの理由で刷新を決断した。
mcframe 7を導入後、生産管理および在庫管理の業務をmcframe 7に合わせることで業務が効率化され、データの一元化ができたことで内部統制を強化でき、監査に必要なデータの抽出も迅速に行えるようになった。今後はmcframe 7がマルチカンパニーに対応しているため国内外の関係会社1社へ横展開する。
高まるプロジェクトの需要と難易度
求められるスキルとキャパシティ
独立採算制で情報がサイロ化していた事業部ごとの正確な収支の可視化、製品ごと、取引先ごとの実際原価の把握、分断されていた生産と営業間の情報連携などをmcframe 7のSCMおよびPCMで実現したのは化粧品OEMをはじめとした多種多様な製品の製造を手掛ける企業だ。
従業員数1,000名、売上高200億円の同社では生産管理をシステム化しておらず、基幹業務システムから必要なデータを手作業で収集し、Excelなどで加工して生産管理と原価管理を行っていた。また独立採算制で情報がサイロ化しており、事業部と工場間の連携が難しく、製品や取引先ごとの原価を把握できないなどの課題があった。
国内の製造業におけるデジタル化への関心が高まる中、提供する側の課題も明確化している。吉原氏は「従来は老朽化したシステムの刷新が主な目的であることが多かったため、求められていたのは安定したシステム構築力でした。現在はDXや変革への期待の高まりから、お客さまにとって必要なデジタル化とは何かを考えて、DXの障害を取り除くための業務変革を共に進め、ときには直言するなど、DX化に向けて継続的に寄り添うパートナーシップが求められています。良い意味でプロジェクトの難易度が上がっており、ベンダーである当社や販売・構築に携わるパートナーにはスキルアップや意識の変革が求められています」と説明する。
プロジェクトの難易度が上がる一方で、対応できるエンジニアのリソースは限られる。エンジニアのスキルアップ、育成に加えて、顧客対応ではその満足度を維持・向上させつつ効率化することが求められている。同社はパートナーに向けてeラーニングでトレーニングプログラムを提供しているほか、同社とパートナーが連携した支援体制など、サービス品質の向上と機会損失の削減に向けた取り組みを進めている最中だ。
今後のビジネスの拡大に向けて、また日本の製造業のデジタル化の促進に向けて小野氏は「多くのお客さまにとってDXは未知の世界ですから、まずは不安を払拭してデジタル化への精神的なハードルを落とすことが重要だと考えています。さまざまなケースの事例やmcframeシリーズのメリットを、インターネットなどメディアを通じて情報発信し、お客さまに気付いていただくことでデジタル化を促進していきます」と語る。